Understanding Drill Bit Geometry:
Key Factors for Choosing the Right Bit
When selecting a drill bit, understanding its geometry can greatly improve your ability to match the bit to your project’s needs. Drill bit geometry encompasses the shape and angles of the bit’s cutting edge, flutes, and tip. These elements determine how efficiently a bit cuts, how well it removes material, and its overall durability. Here’s a guide to drill bit geometry and how it affects performance.
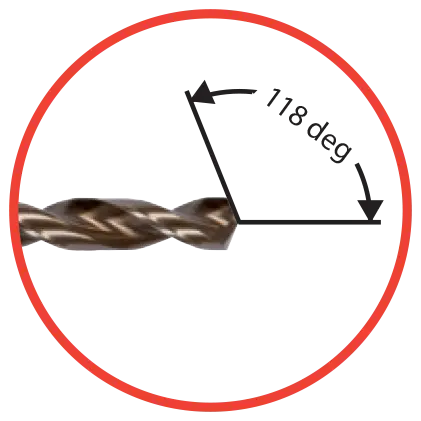
Point Angle
The point angle, or the angle of the bit’s tip, plays a significant role in determining which materials a drill bit can handle effectively:
- 118-Degree Point Angle: The most common point angle for general-purpose drilling, typically used for softer materials like wood and plastic. It provides a sharp, aggressive tip that allows faster cutting with lower force. However, in harder materials like metal, this angle can cause wandering if not properly centered.
- 135-Degree Point Angle: A flatter, more robust angle that is well-suited for harder materials, especially metals. It provides more stability, resists wandering, and works well in applications where precision is essential. This angle is often found on cobalt or titanium-coated bits intended for metal drilling.
- Split Point: Split-point bits have a chiseled tip that self-centers, reducing the need for a pilot hole. They are highly effective for drilling into metal, as they prevent the bit from walking and provide clean entry points.
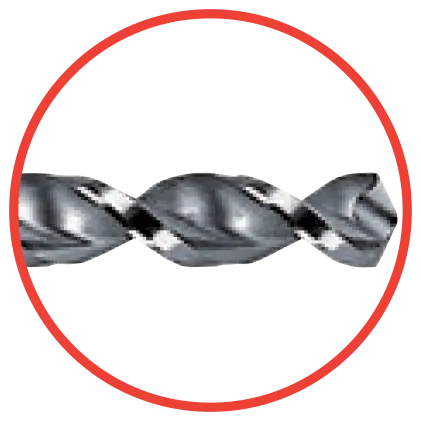
Flute Design
Flutes are the spiral grooves that run along the length of the bit, designed to remove chips and debris as the bit drills into the material. The shape and width of the flutes impact the bit’s ability to clear waste and influence its speed and stability:
- Standard Twist Flutes: Most common in general-purpose twist bits, these flutes are designed to balance speed and chip removal. They work well in wood, plastic, and light metals.
- Deep Flutes: Wider or deeper flutes are often found on bits intended for softer materials or deep drilling applications. They allow faster chip removal, reducing the chance of clogging, which is especially useful in woodworking or when drilling deeper holes.
- Straight Flutes: Some bits, particularly those for masonry, may have straight flutes instead of a spiral design. This type of flute is effective for drilling into harder materials like brick or concrete, providing stability and reducing breakage under high-torque applications.
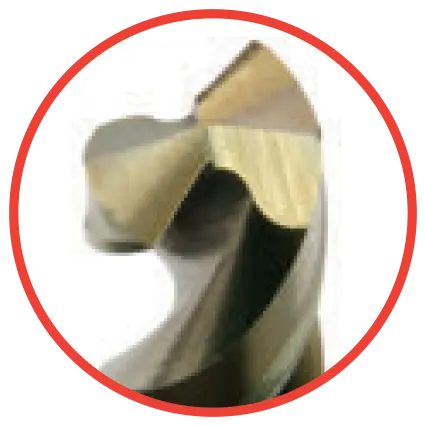
Lip Relief Angle
The lip relief angle is the angle between the cutting edge of the drill and the material. It impacts the cutting efficiency and the smoothness of the drilling process:
- Small Lip Relief Angle (12-15 Degrees): Common for harder materials like metal. This angle provides a sharper cutting edge but reduces wear on the bit, allowing it to hold up longer against tough materials.
- Large Lip Relief Angle (15-20 Degrees): Used for softer materials like wood. This angle enables faster cutting with less resistance but may wear out faster if used on hard materials.
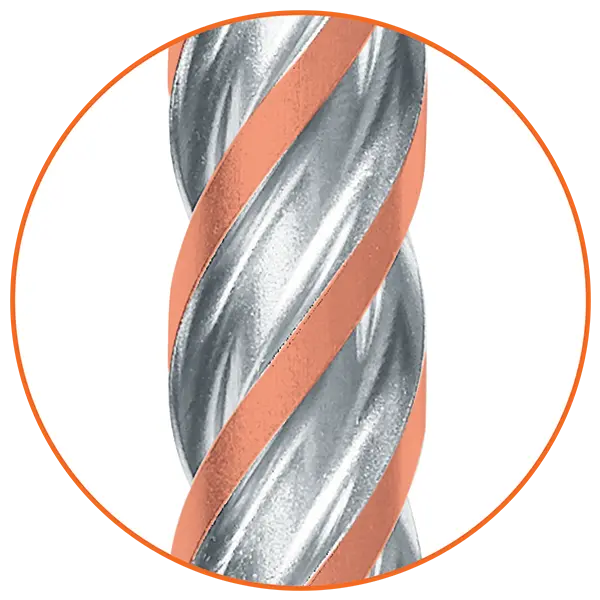
Chisel Edge
The chisel edge is the flat area between the cutting edges on a standard twist bit. Its main function is to center the drill bit and start the drilling process, but it doesn’t actively cut, which can sometimes result in greater force required to penetrate the material. Several variations improve chisel performance:
- Reduced Chisel Edge: Some bits feature a reduced chisel edge or split point to make starting easier, particularly in metal drilling. This minimizes the force needed to begin the hole and reduces the risk of the bit wandering.
- No Chisel Edge (Brad Point): Woodworking bits, especially brad point bits, have no chisel edge. Instead, they have a sharp center point and spurs that allow the bit to start precisely without wandering.
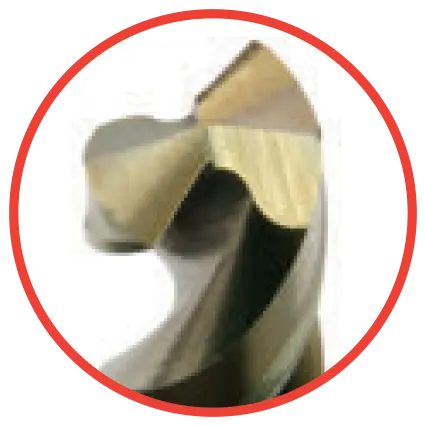
Web Thickness
The web thickness refers to the core thickness of the drill bit. Thicker webs add strength but can make the bit harder to sharpen. Web thickness also influences the rigidity of the bit:
- Thick Web: Bits with a thicker web are stronger and more durable, ideal for heavy-duty applications in tough materials. However, they tend to create more friction and require more force.
- Thin Web: A thinner web is common in bits for softer materials or for bits designed for faster drilling speeds. They produce less resistance and are easier to sharpen, making them suitable for lighter applications.
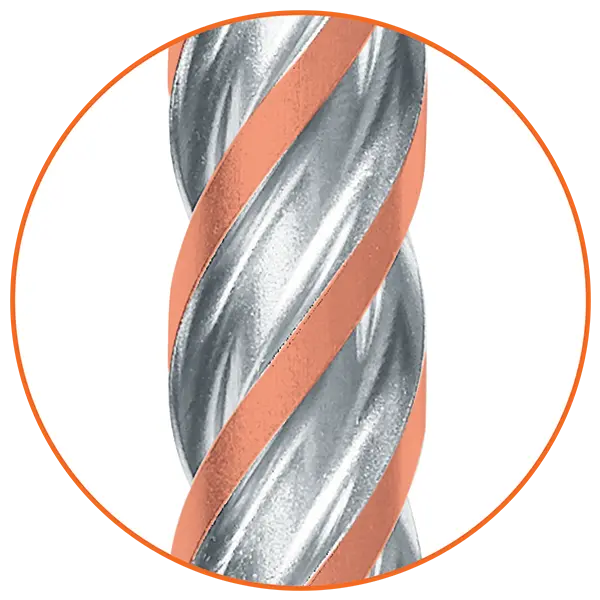
Coatings and Materials
While not technically part of geometry, coatings on drill bits (like titanium, black oxide, or cobalt) impact the bit’s performance, enhancing heat resistance and reducing friction. These coatings and materials influence the bit’s durability, which, combined with geometry, can extend the bit’s lifespan and cutting efficiency.
Choosing Drill Bit Geometry Based on Application
Based on your project’s material and requirements, here’s a quick guide to choosing drill bit geometry:
- Woodworking: For wood, choose a bit with a 118-degree point angle, brad point, and deep flutes for fast chip removal. A thinner web helps with lighter materials, providing cleaner cuts without overheating.
- Metalworking: For harder metals, a 135-degree point angle, thicker web, and flatter lip relief angle offer the durability needed for heavy-duty applications. A split-point tip is ideal for centering and precise entry without wandering.
- Masonry and Concrete: For masonry, straight flutes and carbide tips work best with hammer drills. These bits have durable, flatter points designed to withstand impact and resist wear.